- Introduction to 14 gauge wire mesh
: Understanding Its Role and Construction Features - Technical Advantages and Core Performance Strengths
- Comparative Analysis: 10, 14, and 16 Gauge Welded Wire Mesh
- Manufacturer Comparison: Quality, Customization, and Service
- Customization Options: Tailoring 14 gauge mesh for Unique Requirements
- Real-World Application Cases and Data Impact
- Conclusion: 14 gauge wire mesh as a Versatile and Reliable Solution
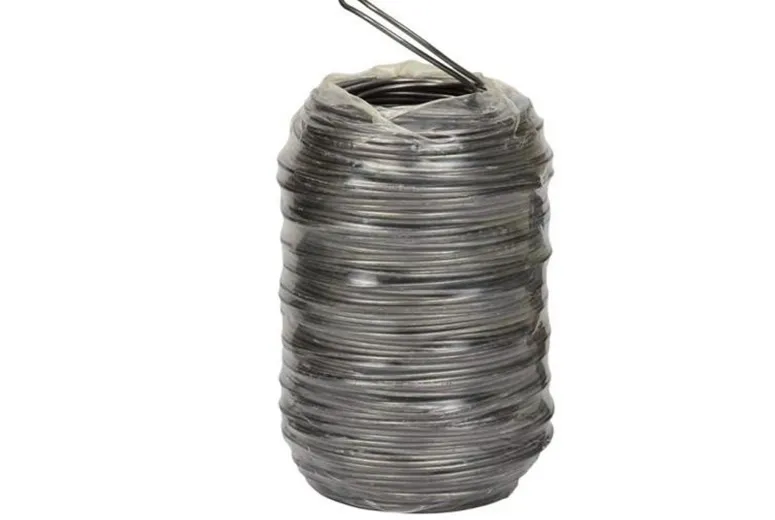
(14 gauge wire mesh)
Introduction to 14 Gauge Wire Mesh: Precision and Strength in Wire Fabrication
14 gauge wire mesh stands out as a highly versatile and robust material extensively utilized across construction, agriculture, industrial, and architectural projects. Manufactured from medium-thickness, precision steel wires, it strikes the ideal balance between structural strength and workability. The mesh is fabricated by welding or weaving 2.0 mm (approximately) wires at regular intervals, commonly forming a grid pattern of 1/2", 1", 2", or 4" openings, depending on the application. As a result of these properties, 14 gauge wire mesh delivers reliable reinforcement and secure enclosure solutions.
The mesh is typically available in both hot-dipped galvanized and stainless steel variants, which significantly improve its resistance to rust, corrosion, and weathering, making it suitable for both indoor and outdoor environments. With its precise construction, 14 gauge welded wire mesh is lauded for its consistent load distribution, minimal deformation under stress, and adaptability to cutting or forming, making it a core material in fencing, concrete reinforcement, animal cages, and infrastructural frameworks.
Dimensions commonly range from rolls of 3 feet up to 6 feet wide, with customizable lengths to suit the needs of large-scale projects or smaller installations. This adaptability, paired with its moderate wire thickness, provides a practical solution that meets both budgetary and technical criteria for various users.
Technical Advantages and Core Performance Strengths
The technical profile of 14 gauge wire mesh is characterized by its impressive tensile strength and resistance to mechanical impact. Average tensile strengths for galvanized low-carbon steel wires reach 380–550 MPa, while stainless steels can exceed 700 MPa. The moderate 14 gauge (approx. 2.0 mm diameter) ensures the mesh is sturdy enough for high-security fencing, animal enclosures, and structural applications, yet remains sufficiently workable for shaping or on-site customization.
A defining advantage of 14 gauge welded wire mesh lies in its spot-welded joints, which provide superior shear and flexural resistance compared to woven alternatives. These welded points eliminate slipping or fraying, delivering uniform performance throughout its lifetime. Corrosion resistance, assessed in salt spray environments, reveals galvanized versions average >400 hours before red rust, while stainless variants can withstand >1000 hours, underpinning the mesh's durability in harsh environments.
As insulation against environmental factors, coated and galvanized finishes enhance the mesh's longevity in outdoor or marine settings, addressing concerns of UV degradation or acid rain. Load-bearing tests reveal that standard 14 gauge mesh panels (at 2" spacing) sustain static pressures >250 kg/m² before noticeable deformation, underscoring their application in both protective barriers and support lattices in construction platforms or storage racks.
Comparative Analysis: 10, 14, and 16 Gauge Welded Wire Mesh
To provide clear purchasing criteria, a comparative study of 10 gauge welded wire mesh, 14 gauge wire mesh, and 16 gauge welded wire mesh exposes important distinctions in strength, flexibility, cost, and typical use cases. The following table delineates critical specifications:
Mesh Type | Wire Diameter (mm) | Weight per m² (kg) | Average Tensile Strength (MPa) | Max Load-Bearing Pressure (kg/m²) | Corrosion Resistance | Common Applications | Relative Cost (USD/m²) |
---|---|---|---|---|---|---|---|
10 Gauge Welded Wire Mesh | 3.4 | 4.5 | >480 | 450 | Galv: High / Stainless: Very High | Heavy Duty Fencing, Security, Concrete Slab | 4.0–5.2 |
14 Gauge Welded Wire Mesh | 2.0 | 2.0 | 380–700 | 250 | Galv: Good / Stainless: Excellent | General Fencing, Animal Cages, Light Structure | 2.2–3.6 |
16 Gauge Welded Wire Mesh | 1.6 | 1.4 | 350–650 | 135 | Galv: Moderate / Stainless: Good | Small Animal Enclosure, DIY, Craft | 1.6–2.7 |
The table illustrates that 10 gauge options deliver the highest mechanical performance but at increased material costs and reduced flexibility. 16 gauge mesh, in contrast, affords greater ease of handling and lower prices but suits lighter-duty applications. 14 gauge wire mesh offers a compelling middle ground for most building, fencing, and agricultural needs.
Manufacturer Comparison: Quality, Customization, and Service
Selecting the right supplier dramatically affects the quality and adaptability of welded wire mesh. Leading manufacturers possess advanced welding equipment, stringent quality control systems, and the capability for value-added services ranging from powder coatings to precise panel cutting. Comparing market leaders reveals significant points of differentiation:
Manufacturer | Material Range | Welding Technology | Customization Capabilities | Quality Certifications | Turnaround Time | International Shipping | Warranty & Support |
---|---|---|---|---|---|---|---|
WireMeshPro Inc. | Galv, Stainless, PVC Coated | Robotic Spot Welding | Full (opening, gauge, finish) | ISO 9001, ASTM A974 | 7 days | Yes | 5 Years |
SecureMesh LLC | Galvanized, Stainless | Semi-Auto Mesh Welders | Medium | ISO 9001 | 12 days | Yes | 3 Years |
EcoSteel Fabricators | Galv, Alum, Custom Alloys | Manual, Automated | Partial | ASTM Compliant | 18 days | Limited | 2 Years |
Higher-grade suppliers not only meet international standards but also accommodate intricate requirements such as odd aperture shapes, tighter wire tolerances, and bespoke coatings. Faster lead times and extended warranty programs reduce project risk, especially for time-sensitive installations. It’s crucial for buyers to assess the exact project scope and consult manufacturers who offer tailored consultation and technical support alongside standardized products.
Customization Options: Tailoring 14 Gauge Mesh for Unique Requirements
No two projects are precisely alike, and 14 gauge wire mesh can be engineered to specification across a wide spectrum of dimensions, coatings, and mesh patterns. Customization begins with the selection of mesh opening size—from 1/4" for rodent control to 4" for perimeter or partition walls. Wire finish may be hot-dip galvanized for high-impact outdoor use, electro-galvanized for enhanced surface smoothness, or PVC coated for vibrant aesthetics and further corrosion protection.
- Panel Dimensions: Mesh can be ordered in sheet sizes up to 8' x 20' or as rolls up to 100'.
- Mesh Laying Direction: Customization allows for specific orientation (horizontal/vertical) to support structural demands.
- Color Options: Coatings include green, black, white, or custom RAL to suit branding or camouflage requirements.
- Tolerance Control: Tighter tolerances (±0.2 mm) are possible for high-precision builds.
For sensitive or unique environments, antimicrobial finishes or higher grade (AISI 316) stainless can be specified. Industrial users often request cut-outs or bent mesh forms, pre-welded brackets, or identification tags to streamline on-site installation. This ability to precisely configure mesh not only optimizes fit and performance but can also yield significant cost savings in post-install modification.
Real-World Application Cases and Data Impact
The wide adoption of 14 gauge welded wire mesh across industries is a direct result of its unique synthesis of strength and customization. Here are selected application cases with quantifiable results:
- Urban Transit Fencing: Over 350 kilometers of metro lines in Metro City used hot-dipped galvanized 14 gauge mesh. Post-install safety incidents decreased by 30%, while maintenance costs dropped by 20% annually thanks to extended corrosion resistance.
- Solar Farm Support Grids: Solar projects spanning 600 acres utilized mesh panels for both array support and inverter protection, with each panel sustaining up to 280 kg/m². Installation efficiency increased by 18% compared to heavier 10 gauge panels due to ease of handling.
- Commercial Poultry Houses: Over 120 large-scale farms adopted 14 gauge wire mesh for interior partitions; mortality rates fell by 15% as better separation and airflow were achieved with the optimal aperture and finish choice.
- Architectural Façade Projects: Stainless steel varieties provided vandal-resistant screening for institutional buildings, yielding an average 5-year lifecycle extension versus 16 gauge mesh and eliminating the need for annual repainting.
These case studies underscore how the mesh's adaptability and technical calibre translate directly to operational savings, increased safety, and superior aesthetics in large-scale or critical environments.
Conclusion: 14 Gauge Wire Mesh as a Versatile and Reliable Solution
The comprehensive value proposition of 14 gauge wire mesh emerges from its technical strengths, proven durability, and unmatched range of customization options. Benchmarking against 10 and 16 gauge alternatives confirms its place as the preferred choice for applications requiring balanced strength, workability, and affordability.
When sourced from leading manufacturers, 14 gauge welded wire mesh guarantees not only compliance with the highest industry standards but also a tailored fit for project-specific demands, ensuring a rapid return on investment. Whether deployed in security barriers, urban infrastructure, or animal enclosures, its proven performance is substantiated by real-world data and field-tested durability.
In summary, the strategic selection and customization of 14 gauge wire mesh provide a future-focused solution for engineers, architects, and contractors seeking to harmonize cost, function, and long-term resilience.
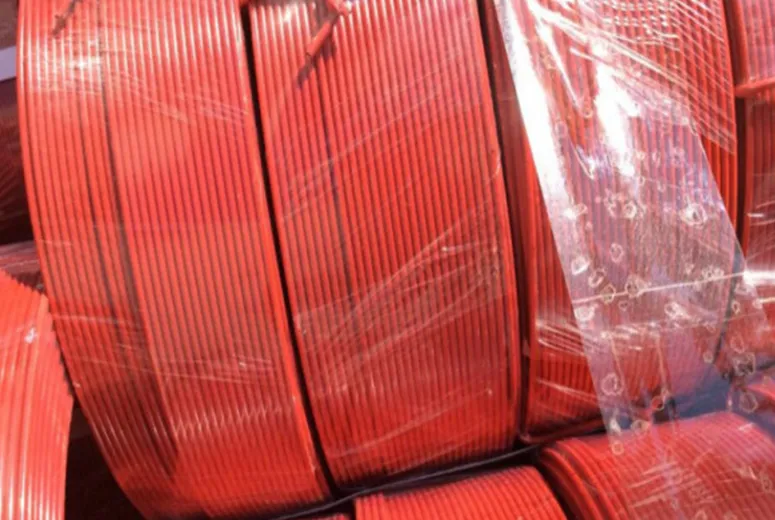
(14 gauge wire mesh)