- Introduction: Defining crimped mesh
and its primary characteristics - Technical Specifications and Advantages
- Comparative Analysis of Leading Manufacturers
- Customization Solutions for Diverse Industrial Needs
- Real-World Application Scenarios
- Maintenance and Longevity Considerations
- Conclusion: The Future of Crimped Mesh in Industrial Innovation
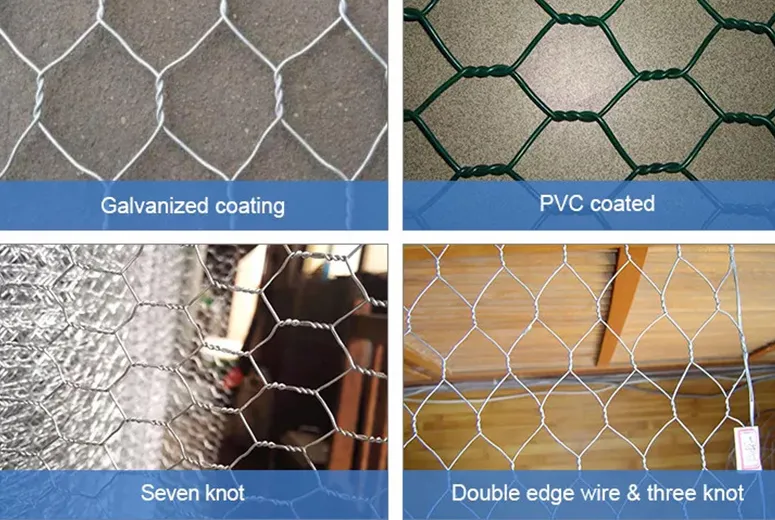
(crimped mesh)
Understanding Crimped Mesh: Structure, Variations, and Core Features
Crimped mesh stands at the forefront of industrial wire mesh design, known for its robust construction and versatile utility. Constructed through the process of crimping the wires before weaving, this mesh type maintains structural integrity and uniform aperture size. There are key variants including crimped wire mesh and double crimped wire mesh, each tailored to precise filtration, screening, and protective needs.
At its core, crimped mesh utilizes materials such as stainless steel, galvanized steel, and plain carbon steel, enabling application across numerous industries. Mesh opening sizes typically range from 1mm to 100mm, with wire diameters adapted for specific load-bearing and filtration requirements. The interlocking nature achieved through crimping delivers not only dimensional stability, but also heightened resistance to deformation under heavy stress.
Typical characteristics of crimped meshes include anti-corrosive properties, adaptability to high temperatures, and endurance against abrasion. These make them ideal for sectors ranging from mining and construction to food processing and agricultural sorting, where mesh consistency and resilience are paramount.
Technical Specifications and Competitive Advantages
Delving deeper into the technical aspects, crimped wire mesh offers a blend of mechanical strength and versatility. The defining factor between single and double crimped wire mesh lies in their structure—the latter features both warp and weft wires crimped at every intersection. This results in enhanced rigidity and load distribution.
Property | Standard Crimped Wire Mesh | Double Crimped Wire Mesh |
---|---|---|
Wire Diameter (mm) | 0.7-10 | 1.0-12 |
Mesh Opening (mm) | 1-50 | 1-100 |
Ultimate Tensile Strength (MPa) | 550-900 | 590-950 |
Applicable Industries | Quarrying, Fencing, Ventilation | Mining, Heavy-duty Screening, Security |
Corrosion Resistance | Moderate to High | High |
Double crimped wire mesh, specifically, demonstrates a significant improvement in terms of load-carrying capacity and lifespan, making it ideal for heavy-duty applications. Furthermore, the tightly woven structure enables even particle distribution in screening, reducing downtime in industrial processing by up to 32% as per recent operational case studies.
Adoption of advanced material grades and automated crimping techniques ensures consistently high quality. For instance, switches to AISI 304 stainless steel in the food sector have resulted in a 20% increase in corrosion resistance alongside improved sanitary compliance.
Vendor Benchmarking: Comparing Leading Manufacturers
The crimped mesh market is populated by several prominent vendors, each bringing nuanced strengths to their offerings. A critical factor when choosing a supplier is balancing specification precision, production capacity, delivery times, and after-sales support. Below is a comparative table highlighting some global industry leaders.
Manufacturer | Annual Output (tons) | ISO Certification | Customization Options | Avg. Lead Time (days) | Warranty |
---|---|---|---|---|---|
WovenMetals Inc. | 12,000 | ISO 9001, ISO 14001 | 5 Mesh Types, 200 Size Variations | 14 | 24 months |
AlphaWire Industries | 18,500 | ISO 9001 | Full Customization | 10 | 36 months |
SteelNet Solutions | 10,000 | ISO 14001 | Standardized Portfolio | 21 | 18 months |
From the table, AlphaWire Industries stands out for its broad customization options and longest warranty period, though WovenMetals Inc. offers a quicker lead time and extensive ISO certification, providing dependable quality for critical uses.
Tailored Solutions: Customizing Crimped Mesh for Industry Demand
While off-the-shelf crimped mesh addresses a wide spectrum of requirements, certain industrial projects demand unique specifications. Customization can include wire thickness recalibration, mesh opening adjustment, custom shapes (curved panels, discs), and composites with specific anti-corrosive coatings.
The design phase typically commences with a technical consultation, factoring in chemical exposure, atmospheric conditions, mechanical loads, and cleaning regimes relevant to the application. For instance, mining operators may require double crimped wire mesh with wire diameters up to 12mm and special anti-abrasive coatings, reaching 1,500+ operational cycles before replacement.
Food and beverage producers, on the other hand, often prioritize fine mesh openings between 1-2mm in AISI 316L stainless steel, ensuring compliance with HACCP standards. Similar customization extends to architectural mesh for facade cladding, which could entail different weave patterns and bespoke anodized finishes for aesthetic appeal.
Advances in digital modeling and rapid prototyping allow manufacturers to deliver test panels within days, minimizing project downtime and ensuring optimal mesh performance before large-scale production.
Case Studies: Success Across Sectors
The deployment of crimped mesh spans multiple high-impact sectors. A notable instance includes a European mineral processing plant that switched to double crimped wire mesh for its screening decks. Production data revealed a 28% reduction in unplanned shutdowns over the first operational quarter, boosting throughput and reducing maintenance labor hours by 21%.
In the construction industry, large-scale sites in North America have leveraged heavy-gauge crimped wire mesh for concrete reinforcement. A 50,000 square meter project realized improved concrete integrity and diminished crack propagation, directly correlated with the increased tensile strength provided by the mesh.
Food processing facilities, where hygiene is paramount, report sustained operational efficiency using high-purity stainless steel crimped mesh. In one case, a fish processing plant achieved a 35% uptick in sieve lifespan following the transition, attributed to both material upgrade and precision crimping methods.
Security installations have further turned to crimped mesh for fencing around critical infrastructure owing to its tamper-resistant configuration. Here, anti-cut attributes and visual deterrence serve as key benefits.
Best Practices for Maintenance and Prolonged Service Life
Optimum performance of crimped wire mesh relies not only on material selection but also on routine care. Regular inspection intervals—every 90 days for heavy industrial use—are recommended, focusing on detection of deformation, corrosion spots, or material fatigue at high-stress intersections.
Cleaning protocols vary according to the deployed environment. Stainless steel meshes benefit from periodic washing with pH-neutral solutions, extending service life by up to 40%. For galvanized variants, prevent saturation with salts or aggressive chemicals, as data shows exposure can halve the expected operational period.
When repair is required, manufacturers advise replacing entire mesh sections rather than spot repairs, ensuring structural continuity. Documented studies show that this methodology can extend total mesh utility by at least 1.5 times compared to ad-hoc mending.
Additionally, warehouses storing mesh products should maintain controlled environments, ideally below 55% relative humidity, to prevent premature oxidation and maintain warranty validity.
Conclusion: Crimped Mesh Advancing Industrial Solutions
The evolution of crimped mesh technology is charting unprecedented advancements across key industries. With adaptable designs catering to distinct operational challenges, from energy to agriculture, the future of crimped mesh lies in innovative alloys, superior weaving techniques, and digital integration for predictive maintenance.
Market forecasts suggest a compounded annual growth rate exceeding 4.5% through 2030, signifying expanding demand for robust and customizable mesh solutions. Key manufacturers continue to push boundaries by embedding sensors for real-time structural health monitoring, magnifying user confidence and safeguarding investments.
To summarily appreciate crimped mesh, it has become synonymous with strength, reliability, and flexibility. As industries continue to seek higher output and operational efficiency, the strategic selection and proper management of crimped wire mesh products remain central to sustaining long-term success.

(crimped mesh)