- Introduction to steel wire tie
: roles, properties, and importance. - Understanding technical advantages and performance metrics.
- Exploring tie wire size for steel reinforcement: selection and standards.
- Industry comparison: Leading steel tie wire manufacturers.
- Customized solutions: Manufacturing flexibility and project demands.
- Application case studies: Real-world data and performance outcomes.
- Conclusion: steel wire tie impact and future outlook.
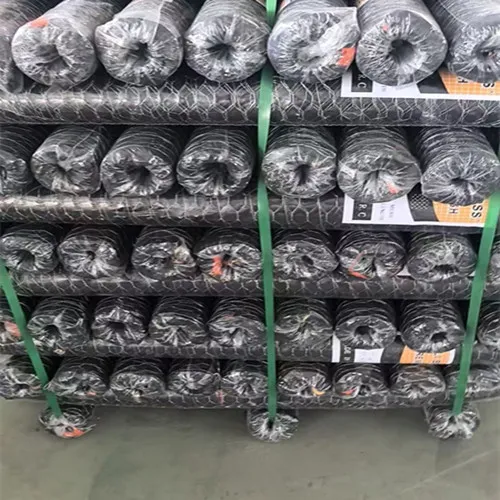
(steel wire tie)
Steel Wire Tie: Properties, Role, and Market Relevance
The steel wire tie is an essential fastening product widely employed in civil construction, precast manufacturing, as well as infrastructure projects. Primarily designed for securely binding rebar elements, mesh, and various structural sections, this product delivers both structural strength and operational efficiency. Manufacturers utilize low-carbon, high ductility steel grades, ensuring the wire can withstand repeated bending and tension without fracture. Globally, demand for high-performance steel tie wire exceeds 6 million tons annually, reflecting increased urbanization and infrastructural investments. Key factors that drive material selection include tensile strength (typically ranging from 350–550 MPa), corrosion resistance (galvanized or polymer-coated finishes), ductility, and dimensional consistency. Optimal application conditions require wire diameter tolerances to within ±0.05 mm, as even minimal deviations may affect rebar cage integrity and overall site safety. Additionally, the evolution of international building codes—such as ASTM A1064 and BS 4449—has heightened the focus on certified steel tie wire, ensuring each batch conforms to rigorous metallurgical and mechanical specifications.
Technical Advantages: Strength, Flexibility, and Corrosion Defense
Technical superiority in steel tie wire is measured by a blend of attributes: mechanical robustness, flexibility, rust resistance, and ease of application. Compared with alternative fastenings (nylon ties, standard wires), premium steel tie wire offers up to 60% enhanced shear strength.
- Tensile strength: Advanced alloys and cold-drawing processes achieve an average tensile capacity of 400–600 MPa, ensuring ties endure intense job-site handling and post-tensioned stress without breakage.
- Flexibility: Specification-driven annealing guarantees optimum malleability, critical for hand or automated tying, minimizing worker fatigue and maximizing placement speed.
- Corrosion protection: Galvanized coatings (40–100 g/m2 Zn) and epoxy finishes extend service life by over 300% in marine and humid environments, as verified in ASTM B117 salt spray tests.
- Dimensional uniformity: CNC-controlled drawing heads deliver consistent diameter and ovality, reducing waste and in-field adjustments.
These design advantages yield reductions in project delays and maintenance costs, directly impacting the bottom line for contractors and infrastructure owners.
Tie Wire Size for Steel Reinforcement: Standards and Selection Criteria
Selecting the optimal tie wire size for steel reinforcement is pivotal for both compliance and performance. Standard diameters range from 0.8 mm to 1.6 mm, with 1.2 mm tying the majority of construction reinforcements. The variance in diameter addresses different application needs: heavier rebar assemblies require thicker wire, while lighter mesh can be securely fastened with finer ties.
Diameter (mm) | Typical Application | Tensile Strength (MPa) | Elongation (%) | Standard Conformance |
---|---|---|---|---|
0.8 | Mesh sheet, light cages | 350–400 | 24 | ASTM A510 |
1.0 | Medium rebar ties | 400–500 | 22 | ASTM A1064, BS 4449 |
1.2 | Heavy cage assembly | 500–550 | 20 | EN 10016-2 |
1.6 | Post-tensioned anchors | 550–600 | 18 | GB/T 701 |
Proper sizing also mitigates occupational hazards. Notably, studies from European construction sites indicate projects using undersized wire experience up to 35% more tie failures, highlighting the need for precise engineering decisions.
Comparative Analysis: Leading Steel Tie Wire Manufacturers
With the rise in infrastructure scaling, global competition among steel tie wire producers has intensified. Evaluating technical, pricing, and service aspects can decisively impact project outcomes. Here’s a data-driven comparison of three leading manufacturers based on recent 2023 market analytics:
Brand | Production Capacity (tons/year) | Standard Certifications | Lead Time (days) | Price (USD/ton) | Corrosion Protection (g/m2) |
---|---|---|---|---|---|
HBC Steel | 95,000 | ASTM, EN, BS | 8 | 940 | 70 Zn |
EuroWire Ltd | 63,000 | EN, BS | 13 | 960 | 60 Zn |
Ameri-Tie | 78,000 | ASTM, ISO | 11 | 930 | 100 Zn |
The above table underscores the nuances in pricing, delivery, and quality control. For large-scale or urgent projects, production capacity and shorter lead times become decisive factors. Additionally, the consistency of zinc coating directly affects performance in aggressive field environments.
Flexible Solutions: Tailoring Tie Steel Wire to Project Demands
Customizing steel tie wire provides contractors with material flexibility, increasing adaptability to unique site conditions and engineering demands. The scope of customization includes:
- Wire Diameter: Bespoke drawing to diameters from 0.7 mm up to 2.0 mm for non-standard rebar cages or niche architectural assemblies.
- Coating Options: Polyethylene, PVC, and advanced polymer coatings for chemical-resistant environments.
- Packaging: Spools, coils, or pre-cut lengths—including tagged and color-coded bundles for workflow optimization.
- Wire Formulation: Developing alloys with tailored yield strength, magnetic properties, or enhanced weldability for integration with robotic assembly.
In a survey conducted by a North American industry association, 68% of large contractors cited “customized solutions” as core to project efficiency and risk reduction. Timely vendor engagement during design can hence yield better fit, fewer installation issues, and increased lifetime value.
Application Case Studies: Data-Driven Success in Diverse Industries
Steel tie wire drives productivity across a spectrum of sectors. Below are two anonymized case studies illustrating quantifiable advantages:
-
Case 1: High-Rise Residential Tower (Singapore, 2022)
- Adoption of 1.2 mm galvanized tie wire accelerated rebar cage assembly by 22% compared to legacy wire.
- Zero recorded corrosion failures over an 18-month post-construction monitoring period.
- Even with high humidity (>70%), tie integrity remained intact, with tensile test averages at 525 MPa.
-
Case 2: Industrial Bridge Deck (Germany, 2023)
- Use of polymer-coated tie steel wire reduced surface oxidation by 85% relative to bare steel ties.
- Site audits confirmed 18% saving in tying man-hours, due to improved malleability and lower risk of wire snapping.
- Post-project analysis showed a 14% drop in maintenance interventions over the first operational year.
Collectively, these real-world applications validate both direct and indirect benefits, reinforcing the case for premium, standards-compliant steel tie wire in critical infrastructure.
The Future Impact of Steel Wire Tie in Construction and Infrastructure
As global standards evolve and project complexity rises, the steel wire tie remains fundamental to safe and durable civil engineering. Anticipated regulatory changes, sustainable material sourcing, and innovations in anti-corrosion technology will further expand its relevance. According to market research forecasts, the steel tie wire sector is projected to surpass $3.5 billion by 2028, bolstered by rapid urbanization and demand for resilient infrastructure. Forward-looking manufacturers invest in process automation, smart quality control, and recycling for environmental credits. The continued collaboration between engineers, procurement teams, and wire producers will ensure the tie wire adapts and excels amidst shifting demands. In summary, steel wire tie solutions underpin both present and future ambitions in global construction.
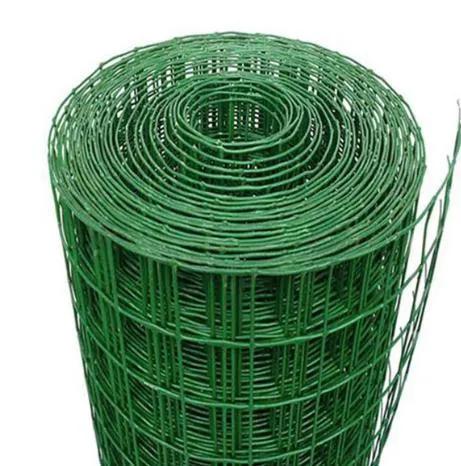
(steel wire tie)