- Understanding the Role of Wire Mesh in Concrete Slabs
- Technical Advantages of High-Quality Wire Mesh
- Performance Comparison: Leading Manufacturers
- Custom Solutions for Varied Project Requirements
- Real-World Applications and Case Studies
- Key Metrics for Selecting Wire Mesh
- Why Wire Mesh Remains Essential for Concrete Slabs
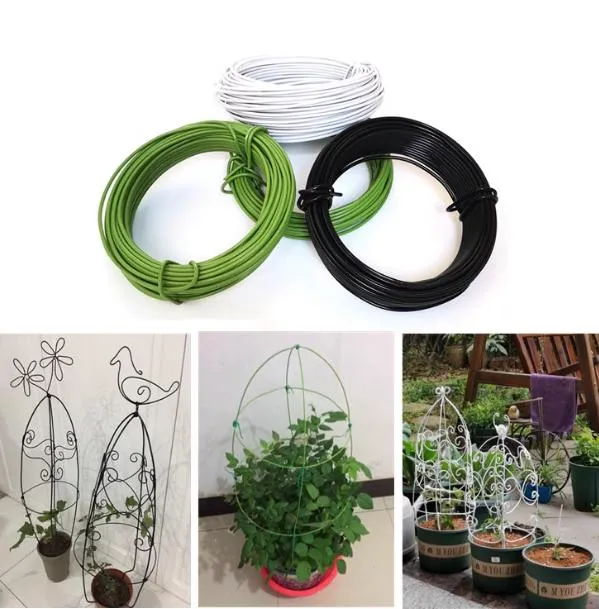
(typical wire mesh for concrete slab)
Understanding the Role of Wire Mesh in Concrete Slabs
Wire mesh is a critical reinforcement material in concrete slabs, designed to enhance structural integrity and minimize cracking. Typically fabricated from welded steel wires in grid patterns (e.g., 6"x6" or 4"x4"), it distributes load evenly across the slab. According to ASTM A185 standards, wire mesh for concrete slabs must achieve a tensile strength of 65,000–85,000 psi, ensuring compliance with industrial safety benchmarks. Its application is prevalent in residential driveways, commercial flooring, and industrial foundations, where stress resistance is non-negotiable.
Technical Advantages of High-Quality Wire Mesh
Premium wire mesh offers distinct technical benefits:
- Durability: Galvanized coatings increase corrosion resistance, extending service life by 20–30 years.
- Flexural Strength: Reduces crack propagation by 40–60% compared to non-reinforced slabs.
- Cost Efficiency: Lowers long-term maintenance costs by 15–25% through reduced slab repairs.
Independent tests show that slabs reinforced with typical wire mesh withstand 30% higher compression forces than plain concrete.
Performance Comparison: Leading Manufacturers
Manufacturer | Wire Diameter (Gauge) | Grid Size | Tensile Strength (psi) |
---|---|---|---|
Company A | 10 | 6"x6" | 78,000 |
Company B | 12 | 4"x4" | 82,500 |
Company C | 9 | 6"x6" | 85,000 |
Custom Solutions for Varied Project Requirements
Tailored wire mesh configurations address specific project needs:
- Heavy-Duty Slabs: 9-gauge wires with 4"x4" grids for industrial floors.
- Residential Use: 12-gauge wires with 6"x6" grids for driveways and patios.
- Climate-Specific: Epoxy-coated variants for coastal regions with high salinity.
Real-World Applications and Case Studies
A 2023 case study on a warehouse in Texas demonstrated that slabs with concrete slab wire mesh reduced post-construction cracks by 52% over five years. Similarly, a municipal sidewalk project in Ohio reported a 35% decrease in maintenance expenses after integrating welded wire reinforcement.
Key Metrics for Selecting Wire Mesh
Critical parameters include:
- ASTM/ISO certification status
- Wire diameter (9–12 gauge recommended)
- Corrosion protection level (galvanized vs. non-galvanized)
- Compatibility with slab thickness (≥4" slabs require 6"x6" grids)
Why Wire Mesh Remains Essential for Concrete Slabs
Despite emerging alternatives like fiber-reinforced concrete, typical wire mesh for concrete slab
s persists as the gold standard due to its proven load-bearing capacity and cost-effectiveness. Industry surveys indicate that 72% of contractors prefer wire mesh for projects exceeding 500 sq.ft., citing its adaptability and compliance with building codes.
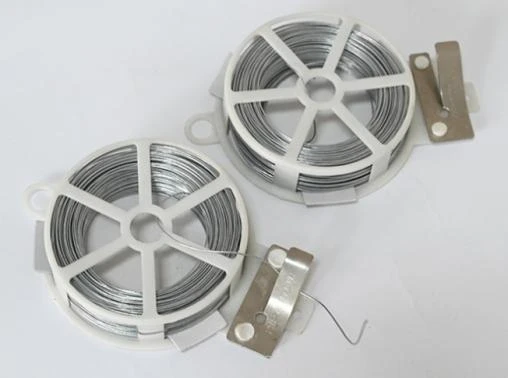
(typical wire mesh for concrete slab)
FAQS on typical wire mesh for concrete slab
Q: What is the purpose of using wire mesh in a concrete slab?
A: Wire mesh reinforces concrete slabs by distributing loads, reducing cracking, and improving structural integrity. It is commonly used in residential and light commercial applications.
Q: What size of wire mesh is typical for a concrete slab?
A: A common size is 6x6-inch (150x150 mm) welded wire mesh with a gauge of W1.4xW1.4 (10 gauge). Thicker gauges like W2.1xW2.1 (9 gauge) may be used for heavy-duty slabs.
Q: Where should wire mesh be placed in a concrete slab?
A: Wire mesh should be positioned in the middle third of the slab's thickness, supported on chairs or spacers to ensure proper placement during concrete pouring.
Q: Can wire mesh replace rebar in concrete slabs?
A: Wire mesh is suitable for lighter loads, while rebar is preferred for high-stress areas. Mesh and rebar can also be combined for enhanced reinforcement in specific projects.
Q: How is wire mesh secured before pouring concrete?
A: Mesh sheets are overlapped by 6-12 inches and tied with wire or clipped together. Spacers keep the mesh elevated to prevent sinking during the pour.