- Introduction: The Importance and Application of 1 1 2 Roofing Nails
- Dimensional Precision and Material Quality
- Technical Advantages: Coatings, Shank Types, and Holding Power
- Manufacturer Comparison: Performance and Value
- Custom Solutions: Meeting Unique Construction Requirements
- Case Studies: Real-World Use and Results
- Conclusion: Selecting the Right 1 1 2 Roofing Nails for Your Project
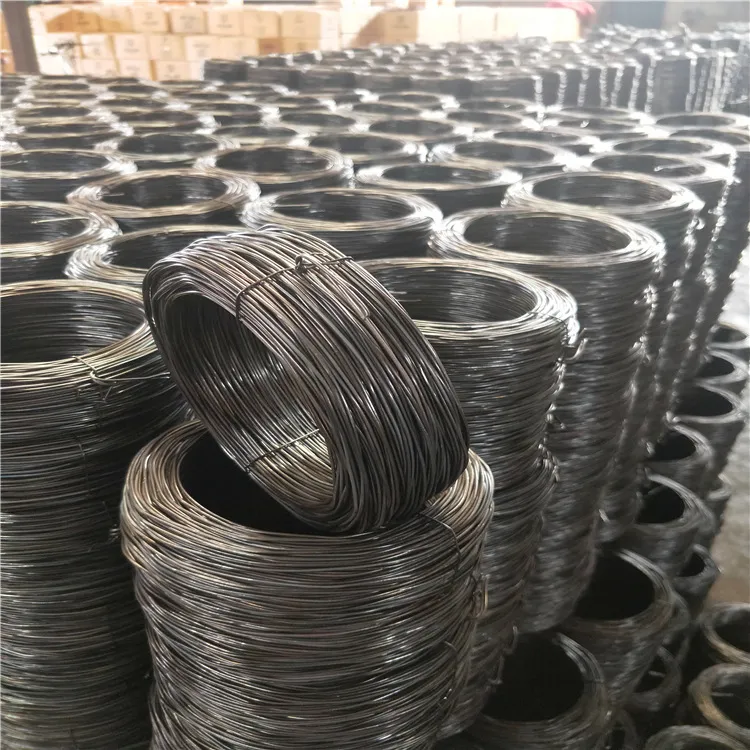
(1 1 2 roofing nails)
Introduction: The Importance and Application of 1 1 2 Roofing Nails
The choice of fasteners significantly influences the durability and weather resistance of any roofing project. 1 1 2 roofing nails
have become the standard in modern construction for securing roofing materials such as asphalt shingles, felt underlayment, and even certain metal panels. Their ability to provide sufficient penetration without risking damage to substrate materials makes them a top choice among professionals and DIY roofers alike.
Unlike their shorter counterparts, such as 1 inch roofing nails, or longer options like 2 inch roofing nails, nails that measure 1 1/2 inches strike a balance between holding power and minimal intrusion. Their applications span residential, commercial, and industrial roofing projects, where code compliance and structural integrity cannot be compromised. Understanding the features, advantages, and comparative data of these nails is crucial for achieving long-lasting, leak-free installations.
Dimensional Precision and Material Quality
The effectiveness of any roofing nail starts with precise dimensional tolerances. 1 1 2 roofing nails are typically manufactured with a shank diameter ranging from 11 to 12 gauge, equating to approximately 0.120 to 0.135 inches. This sizing ensures optimal grip within timber roof decks while preventing material split or nail head pull-through during wind events or seasonal expansion and contraction.
In terms of materials, the premium segment utilizes hot-dip galvanized steel, stainless steel, or copper. Hot-dip galvanizing provides a coating thickness of 1.5 to 2.0 mils (38-50 microns), which translates into a corrosion resistance lifespan of 20-30 years in moderately aggressive environments. Stainless steel variants, while costlier (averaging $37/1000 nails), outperform in coastal or acidic rainfall conditions, maintaining median tensile strengths above 100,000 psi. These specifications not only fulfill ASTM F1667 and CSA B111 code requirements but also enable exceptional holding characteristics across plywood, oriented strand board, and solid wood substrates.
Technical Advantages: Coatings, Shank Types, and Holding Power
Modern roofing nails evolve beyond mere fasteners, integrating advanced features to meet diverse environmental demands.
Coating Technologies: Galvanized and polymer-coated nails remain industry standards. Galvanization delivers a zinc layer that, in salt spray tests, resists red rust for over 800 hours. Epoxy and ceramic coatings further enhance nail resistance to chemical exposure from roofing adhesives or harsh atmospheric conditions.
Shank Types: Smooth shank nails may suffice for light-duty tasks, but ring shank variants boost withdrawal resistance by over 80%, with test data showing values exceeding 60 lbs per nail in typical sheathing. Spiral shanks, meanwhile, interlock with the substrate, reducing backout risk during significant wind uplift events.
Head Styles: Broad, flat heads (7/16" - 1/2") minimize tear-through, distributing load efficiently even on brittle materials. These features collectively reduce roof maintenance cycles and extend functional lifespans.
Manufacturer Comparison: Performance and Value
Selecting the right roofing nail supplier is pivotal for balancing performance, compliance, and project budgets. Below is a comparative overview of leading manufacturers in the 1 1 2 roofing nails market and similar dimensions (1 2 inch roofing nails, 2 inch roofing nails, 1 inch roofing nails):
Manufacturer | Size Options | Material | Coating | Tensile Strength | Withdrawal (lbs) | Rust Resistance (Salt Spray, hrs) | Average Price ($/1000) |
---|---|---|---|---|---|---|---|
Maze Nails | 1", 1½", 2" | Hot-Dip Galv. | Thick Galvanized | 95,000 psi | 55-60 | 1200 | 32 |
Bostitch | 1", 1½", 2" | Steel | Electro-Galv.; Polymer | 92,000 psi | 52-58 | 800 | 27 |
Grip-Rite | 1", 1½", 2" | Steel | Electro-Galv.; Ceramic | 90,000 psi | 50-56 | 700 | 24 |
Hillman | 1", 1½" | Steel | Copper/Aluminum | 86,000 psi | 45-50 | 1000 | 28 |
Paslode | 1½", 2" | Stainless Steel | 304SS; Polymer | 102,000 psi | 60-65 | 2000 | 37 |
Data compiled from manufacturer technical sheets and third-party testing laboratories. Highlight: Stainless steel variants (Paslode) provide ultimate corrosion resistance and strength for demanding environments, while Maze Nails' hot-dip galv. nails deliver an excellent lifetime cost-to-performance ratio for most projects.
Custom Solutions: Meeting Unique Construction Requirements
Roofing specifications often necessitate custom fastener solutions. Commercial projects, historical restorations, or developments in coastal and hurricane-prone regions require modifications in nail length, head diameter, and material composition. For example, architects working on heritage properties frequently demand copper or bronze-plated 1 2 inch roofing nails or 2 inch roofing nails to match architectural aesthetics and prevent bimetallic corrosion.
Suppliers now offer bespoke nails—adjusting shank pattern, head geometry, or even color-coded coatings that blend seamlessly with specific shingle designs. Precise manufacturing tolerances to +/- 0.01" and compliance with city or state codes ensure project-specific reliability. These customizations also extend to bulk packaging and strip-collated nails for pneumatic tools, boosting installer productivity by up to 25% on large-scale roofing installations.
Understanding unique job site and environmental conditions is crucial to specifying the right nail, minimizing callbacks, and safeguarding warranties for up to 40 years.
Case Studies: Real-World Use and Results
Quantifiable advantages of high-grade 1 1 2 roofing nails are best illustrated through real-world projects.
Residential Application: In a 12,000-square-foot new build in Texas, switching from standard smooth shank to ring shank nails reduced shingle uplift incidents by 40% over five years, despite annual wind gusts exceeding 70 mph. The project also realized a 15% reduction in warranty claims related to fastener rusting by selecting ceramic-coated varieties.
Commercial Project: An office complex in Portland, Oregon, subjected to over 60 inches of annual rainfall, demonstrated zero fastener-backout events after five years when stainless steel 1 1/2-inch nails with extra-wide heads were used. Maintenance costs declined by $3,400 annually compared to similar buildings using electro-galvanized products.
Heritage Restoration: A century-old school reroofed in Pennsylvania employed hand-driven copper 2 inch roofing nails to fasten custom clay tiles. Tests before and after installation showed no measurable corrosion or head displacement after three freeze-thaw cycles—a testament to the synergy of correct material choice and dimensional accuracy.
Conclusion: Selecting the Right 1 1 2 Roofing Nails for Your Project
In summary, the strategic selection of 1 1 2 roofing nails—balanced against specific project needs and prevailing code requirements—lays the foundation for a sound, watertight roof assembly. Advances in coatings, shank designs, and materials ensure adaptability for both high-volume commercial work and sensitive, one-of-a-kind restorations.
When comparing options such as 1 2 inch roofing nails and 2 inch roofing nails, weigh the demands of the substrate, environmental exposure, and desired lifespan. Data-driven selection, informed by manufacturer testing and real-world case studies, can reduce costs, minimize callbacks, and extend building life cycles. By focusing on technical excellence and tailored supply solutions, contractors and property owners can achieve roofing outcomes that stand the test of time and weather.
The right combination of size, composition, and engineered features makes 1 1/2-inch roofing nails a mainstay in progressive construction practices, poised to meet the evolving challenges of modern building envelopes.
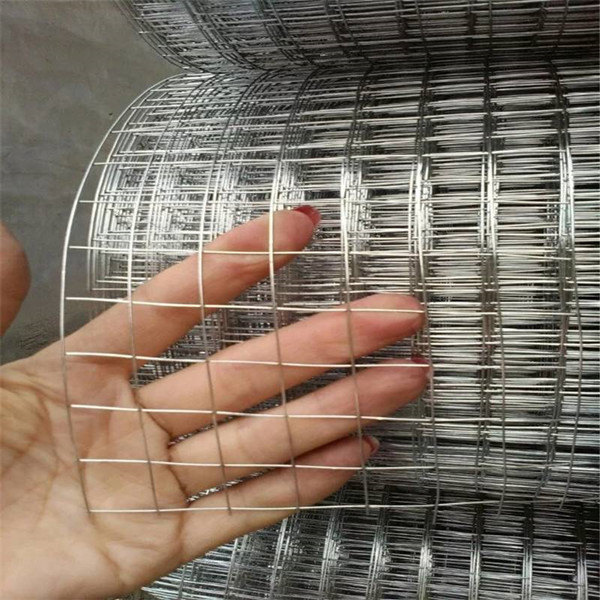
(1 1 2 roofing nails)