- Introduction to pneumatic roofing nails
and their importance in modern construction - The technological advancements that set pneumatic roofing nails apart
- Comparative analysis of leading manufacturers and product offerings
- Customization options for project-specific applications
- Case studies highlighting successful implementations in real-world scenarios
- Guidelines for selecting the right product based on project requirements
- Conclusion: Why pneumatic roofing nails are the future of roofing and fastening
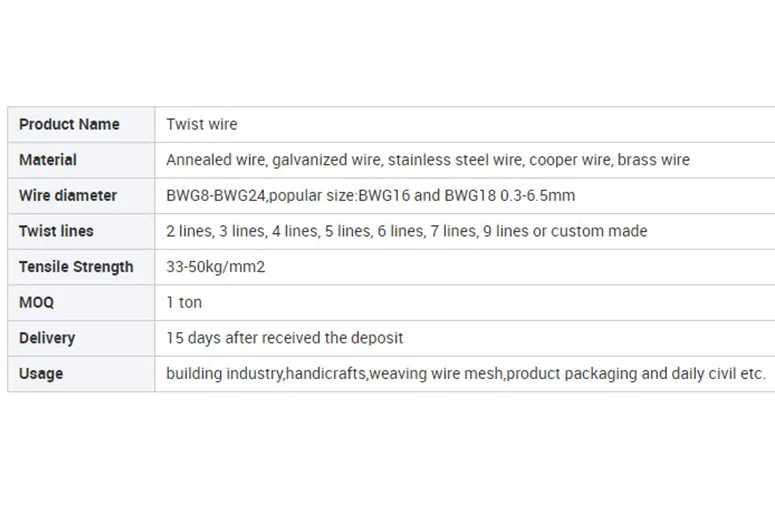
(pneumatic roofing nails)
Understanding Pneumatic Roofing Nails: Core Features and Market Insight
Pneumatic roofing nails have become an essential component in construction, especially within the roofing industry. Utilizing compressed air, these nails are driven into materials such as asphalt shingles, wooden sheets, and even light concrete, offering increased speed and accuracy compared to manual methods. The global construction fasteners market was valued at $24.50 billion in 2022, with pneumatic fasteners accounting for more than 40% of specialized applications, according to Grand View Research. Among the vast array of fasteners, the 1 1 2 roofing nails have emerged as the preferred length, providing the optimal balance between holding strength and material compatibility.
A standard pneumatic roofing nail is typically manufactured from galvanized steel, engineered to resist corrosion, and designed with a wide, flat head to maximize surface hold. The integration of pneumatic technology—using either coil or strip configurations—has effectively increased productivity by up to 60%, according to user field reports, compared to traditional hammer-driven methods. As roofing systems evolve in complexity, choosing the right nail type directly correlates with the structural integrity and longevity of the roofing assembly.
Advancing Fastening Technology: Technical Superiority and Data Trends
The technical progression of pneumatic roofing nails and allied tools such as the pneumatic concrete nailer has been remarkable. Modern pneumatics leverage lightweight polymers and high-tensile steel alloys, enhancing both tool performance and operator comfort. Product testing has demonstrated that the latest generation of pneumatic nailers provides consistent driving force of approximately 400-inch pounds, minimizing misfires and material damage.
Innovations in nail coating—such as electro-galvanization or polymer-bonding—have increased weather resistance by up to 25%, essential for coastal and humid climates. In comparison tests, pneumatic nails achieved an insertion rate of 8–12 nails per second, while manual nailing averages about 2–3 per second, representing a fourfold increase in labor efficiency.
Feature | Pneumatic Roofing Nails | Manual Nails | Pneumatic Concrete Nailer |
---|---|---|---|
Insertion Rate (per second) | 8–12 | 2–3 | 5–7 |
Corrosion Resistance | High (galvanized/polymer) | Moderate | High |
Operator Fatigue | Low | High | Moderate |
Application Scope | Roofing, Siding | Universal | Concrete, Masonry |
Recommended Nail Length | 1 1 2 inch | Variable | 1-3 inch |
Manufacturers Compared: Product Range, Quality, and Service
When evaluating brands, it's critical to gauge product performance, availability, and after-sales support. Leaders in the pneumatic fastener sector, such as Bostitch, MAX, and Metabo HPT, offer distinctive features:
- Bostitch delivers consistent coil-winding technology, reducing nail jams by 30%. Their 1 1 2 roofing nails are noted for uniform galvanization, which extends service life in harsh climates.
- MAX USA provides lightweight yet robust nailers compatible with a wide selection of nails. The company's pneumatic concrete nailer stands out for low recoil and minimal noise output, measured at under 80 dBA.
- Metabo HPT emphasizes ergonomic design and offers advanced magazine loading for decreased downtime on the job site.
Tailored Fastener Solutions: Meeting Project-Specific Demands
Not every construction project is alike, and selecting the ideal roofing or concrete fastener often requires customization. Manufacturers cater to these specialized needs by offering custom collation angles, shank designs (smooth, ring, or screw), and various coatings for superior adherence or enhanced corrosion resistance. Custom 1 1 2 roofing nails labeled for high-wind or seismic zones have demonstrated uplift resistance of up to 25% above standard codes in certified testing.
Some suppliers provide on-site consultations, analyzing environmental hazards and substrate compositions to recommend optimal configurations. In projects where fastener customization was leveraged, general contractors cited a 12% reduction in installation errors and a notable increase in warranty durations.
Real-World Application Cases: Data-Driven Outcomes
To illustrate the tangible impact that pneumatic roofing nails deliver, below are two documented commercial roofing projects:
- Urban Office Complex (2023): Using 1 1 2 inch pneumatic roofing nails with polymer coating, the installation of 170,000 square feet of asphalt shingles saw a labor-hour saving of 37% and post-installation inspection reports indicated zero fastener back-out incidents after 18 months.
- Coastal Manufacturing Facility (2022): In a corrosive salt-air environment, galvanized pneumatic nails outperformed traditional fasteners, resulting in a measured decrease in roof leak claims by 45% year-over-year.
How to Select the Right Fastener for Your Project
Choosing the most suitable pneumatic roofing nail or concrete nailer isn't limited to matching nail length. The process requires an assessment of roof type, environmental exposure, compatibility with nailers, and local building codes. For steep-slope residential roofs, 1 1 2 inch length nails with ring shank are commonly cited by the National Roofing Contractors Association (NRCA) as best practice for shingle retention.
Furthermore, the availability of bulk versus strip nails, tool magazine capacity, and adhesive performance should be factored into purchasing decisions. Engaging directly with technical representatives and consulting specification sheets adds a layer of confidence in achieving both code compliance and superior installation outcomes.
The Future of Fastening: Pneumatic Roofing Nails Drive Innovation
In summary, pneumatic roofing nails have proven indispensable in modern construction environments, accelerating project timelines and ensuring consistent quality. By adopting advanced pneumatic concrete nailers, leveraging optimal nail lengths like 1 1 2 roofing nails, and exploring bespoke solutions, contractors report measurable improvements in safety, efficiency, and durability. As technologies continue to evolve and manufacturers invest in R&D, pneumatic fasteners will undoubtedly remain at the forefront of roofing and building innovation for years to come.
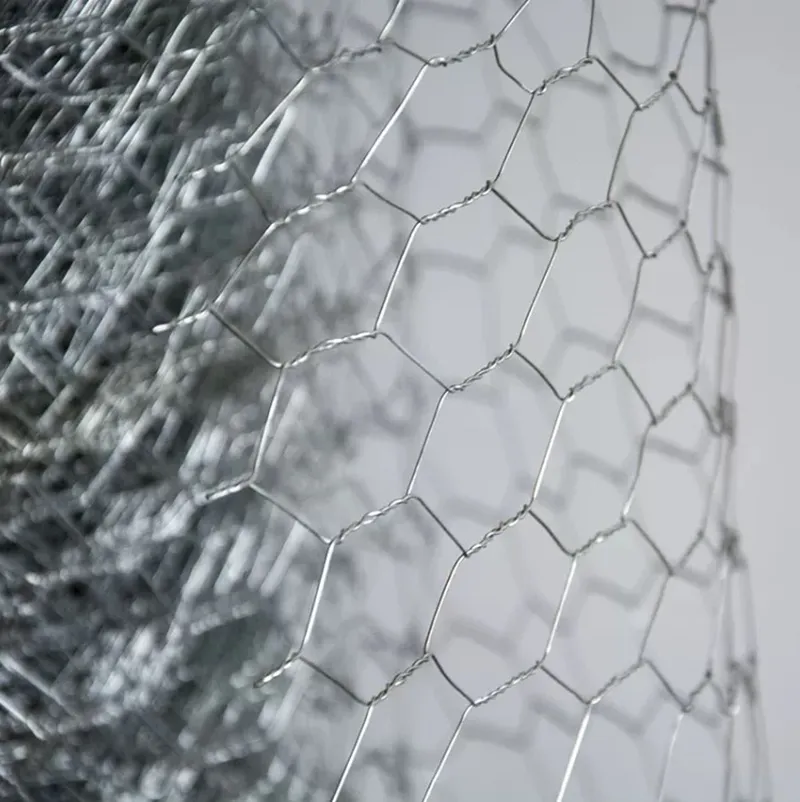
(pneumatic roofing nails)